A cordless drill is a versatile, portable tool used for drilling holes and driving screws. It consists of several parts including a motor, chuck, and battery. There are two main types of motors: brushed and brushless, each with its own benefits. Cordless drills can be equipped with various attachments for different tasks. Major brands include DeWalt, Makita, Bosch, RYOBI, and Hercules. Before cordless drills, people used manual drills and corded electric drills. Hercules drills, available at Harbor Freight, are known for their affordability and performance.
History of Drills: From Manual to Cordless
Before diving into the specifics of modern cordless drills, it’s essential to understand their evolution:
History of Manual Drills
Manual drills have a rich history, tracing back thousands of years. These tools were essential for many early civilizations and have evolved significantly over time.
- Bow Drill (Ancient Times)
- The bow drill is one of the earliest types of drills, dating back to the Upper Paleolithic era, around 10,000 BCE. It was used primarily for starting fires and drilling small holes in materials like wood, stone, and bone. A simple yet effective design, it consisted of a bow, a string, a spindle, and a bearing block
- The bow drill is one of the earliest types of drills, dating back to the Upper Paleolithic era, around 10,000 BCE. It was used primarily for starting fires and drilling small holes in materials like wood, stone, and bone. A simple yet effective design, it consisted of a bow, a string, a spindle, and a bearing block
- Brace and Bit (Middle Ages)
- The brace and bit became popular in the Middle Ages and remained widely used until the advent of modern power tools. This tool consists of a U-shaped brace that rotates to drive a bit into the material. It allowed for greater torque and efficiency, making it possible to drill larger holes more easily.
- The brace and bit became popular in the Middle Ages and remained widely used until the advent of modern power tools. This tool consists of a U-shaped brace that rotates to drive a bit into the material. It allowed for greater torque and efficiency, making it possible to drill larger holes more easily.
- Eggbeater Drill (19th Century)
- The eggbeater drill, developed in the 19th century, is a hand-cranked drill that resembles an eggbeater. It offered greater control and precision, suitable for smaller and more delicate work. This type of drill remained popular for light woodworking and hobbyist projects.
- The eggbeater drill, developed in the 19th century, is a hand-cranked drill that resembles an eggbeater. It offered greater control and precision, suitable for smaller and more delicate work. This type of drill remained popular for light woodworking and hobbyist projects.
- Hand Augers and Gimlets
- Hand augers and gimlets were also common manual drilling tools. Augers were used for larger holes, often in woodworking and construction, while gimlets were for smaller, more precise holes.
Usage of Manual Drills
Manual drills are still valued for their simplicity, control, and precision, especially in certain specialized applications.
- Woodworking
- Many woodworkers prefer manual drills for delicate tasks where precision is crucial. They are ideal for drilling small holes for screws and dowels without the risk of splitting the wood.
- Hobbyist Projects
- Hobbyists and model makers often use manual drills for tasks that require fine control and attention to detail.
- Manual drills are perfect for working with small, fragile materials like plastics and metals in model making.
- Traditional Crafts
- In traditional crafts such as boat building and furniture making, manual drills are still used to maintain authenticity and craftsmanship. The slower speed and tactile feedback of manual drills allow for a level of control that power drills can’t match.
- Remote Locations
- Manual drills are useful in remote or off-grid locations where electricity is unavailable or unreliable. They are reliable, requiring no power source other than human effort.
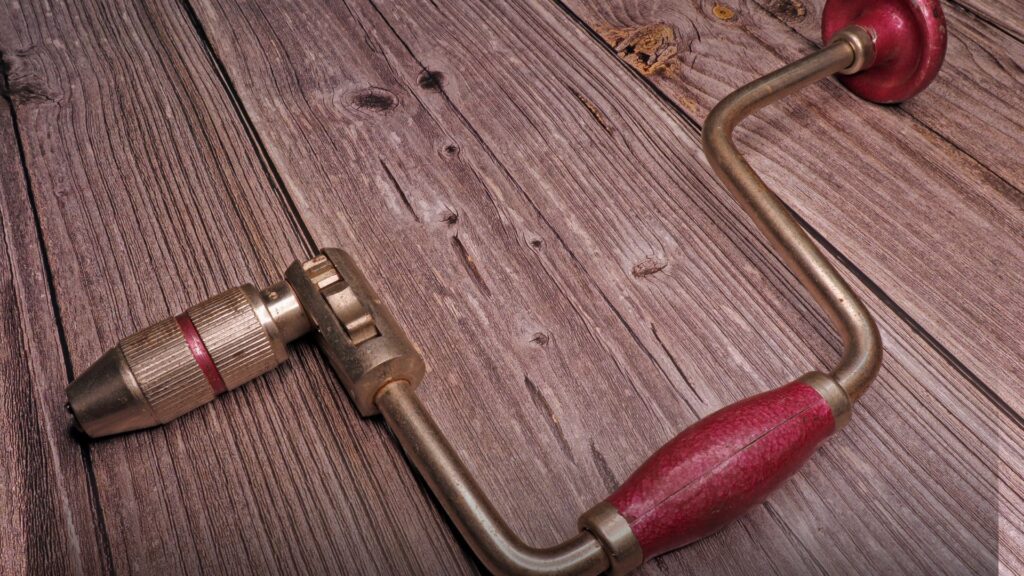
- Corded Electric Drills: Introduced in the early 20th century, these drills offered more power and consistency than manual versions. However, they were limited by the length of their power cords, which restricted mobility.
The development of cordless drills revolutionized these tools by combining the power of electric drills with the portability of manual ones.
Parts of a Cordless Drill
Understanding the components of a cordless drill helps in using and maintaining it effectively:
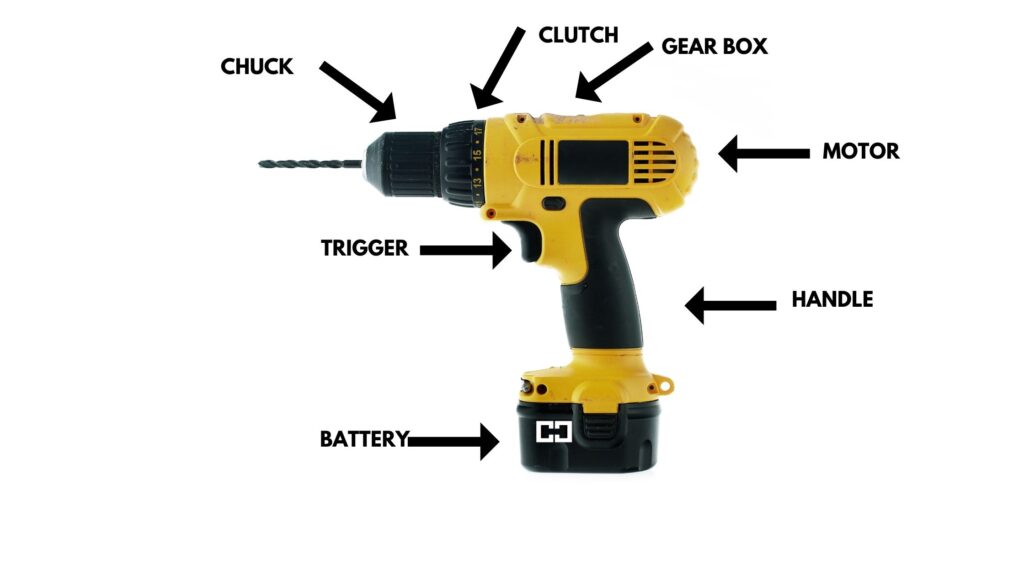
- Motor: The heart of the drill, converting electrical energy into mechanical motion.
- Brushed Motor: Uses carbon brushes to transfer electricity to the motor windings.
- Brushless Motor: Uses electronic controllers to distribute power, offering better efficiency and durability.
- Chuck: The part that holds the drill bit or attachment. Common types include:
- Keyed Chuck: Requires a key to tighten or loosen the drill bit.
- Keyless Chuck: Allows bit changes by hand, without needing a tool.
- Battery: Powers the drill, usually rechargeable lithium-ion batteries that offer high energy density and long life.
- Trigger: Activates the motor and controls the speed of the drill.
- Gearbox: Allows the drill to operate at different speeds and torque settings.
- Handle: Ergonomically designed for a comfortable grip.
- Clutch: Adjusts the torque setting to prevent over-driving screws or damaging materials.
Brushed vs. Brushless Motors
- Brushed Motors:
- Pros: Generally cheaper, simpler design, and easier to repair.
- Cons: Less efficient, generate more heat and wear out faster due to friction.
- Brushless Motors:
- Pros: More efficient, produce less heat, longer lifespan, and require less maintenance.
- Cons: More expensive due to complex design and electronics.
Major Drill Brands
Several brands dominate the cordless drill market, each offering unique features:
- DeWalt: Known for durability and high performance, ideal for professional use.
- Makita: Offers a wide range of tools with excellent battery life and power.
- Bosch: Combines quality with innovative features and ergonomic design.
- Milwaukee: Popular for their power, advanced technology, and robust construction.
- RYOBI: Affordable and reliable, suitable for both DIY enthusiasts and professionals, with a broad range of tools.
- Hercules (Harbor Freight): A budget-friendly brand providing good performance and reliability for DIY enthusiasts and professionals.
Drill Attachments
Cordless drills are incredibly versatile tools, capable of performing a wide range of tasks with the right attachments. Below is a detailed list of common attachments and their uses:
Drill Bits
- Twist Bits: The most common type of drill bit, can be identified by a cylindrical shaft with helical grooves. Suitable for drilling holes in wood, metal, plastic, and other materials.
- Brad Point Bits: Features a pointed tip and spurs on the edges to ensure clean, precise holes. These bits are ideal for woodworking because they reduce splintering and ensure a smooth finish.
- Masonry Bits: Have a carbide tip to withstand the hardness of materials like brick, stone, and concrete. You’ll need these for drilling into masonry and concrete surfaces.
- Spade Bits: Flat, paddle-shaped bits with a sharp point for larger diameter holes. Commonly used in woodworking for rough, fast drilling.
- Forstner Bits: Features a flat bottom and circular rim with cutting edges. Creates clean, flat-bottomed holes in wood, ideal for cabinetry and woodworking.
- Auger Bits: These have a screw tip to pull the bit into the wood, with large flutes for waste removal. Great for deep, large-diameter holes in wood.
- Step Bits: Cone-shaped with stepped diameters for drilling multiple hole sizes with one bit. These are often used for drilling in thin materials like sheet metal and plastic.
- Hole Saws: Ring-shaped saws with a central bit to guide the hole cutting that create large diameter holes, often used for plumbing, electrical, and carpentry applications.
Screwdriver Bits
- Phillips Head Bits: Cross-shaped tip designed to fit Phillips head screws. Common for general-purpose screw driving in woodworking and construction.
- Flathead (Slotted) Bits: Flat, single-slot tip. Used for slotted screws, found in older applications and simple construction.
- Torx Bits: Star-shaped tip, also known as star bits. They provide better torque transfer and are used in automotive and electronic applications.
- Hex (Allen) Bits: Hexagonal tip used for driving bolts and screws with hexagonal sockets, common in furniture assembly and mechanical applications.
- Pozidriv Bits: Similar to Phillips but with additional cross slots for better grip. Provides more torque and less cam-out, used in European woodworking and construction.
Specialty Bits
- Nut Drivers: Hexagonal sockets designed to drive nuts and bolts. Used in automotive, appliance repair, and construction.
- Impact Driver Bits:
- Designed to withstand the high torque of impact drivers. Used for heavy-duty applications, such as driving large screws and bolts.
- Right Angle Attachments:
- Allows the drill to operate at a 90-degree angle. Useful for drilling or driving in tight spaces where a standard drill cannot fit.
- Flexible Shaft Attachments: A flexible extension that can bend around corners and reach tight spaces. Provides access to hard-to-reach areas.
Cleaning and Polishing Attachments
- Wire Brushes: Made of metal bristles, available in various shapes and sizes. Used for cleaning rust, paint, and debris from metal surfaces.
- Sanding Drums: Cylindrical sandpaper attachments.
- Polishing Pads: Soft pads made of foam or cloth. Used for polishing and buffing surfaces to a high shine. Used for sanding and smoothing wood, plastic, and metal surfaces.
Mixing Attachments
- Mixing Paddles: Paddles designed to attach to the drill. Used for mixing paint, mortar, plaster, and other viscous materials.
Other Attachments
- Countersink Bits: Bits that create a conical hole for countersunk screws. Used to allow the screw head to sit flush with or below the surface of the material.
- Deburring Bits: Bits with sharp edges for removing burrs from drilled holes. Used to clean up and smooth the edges of drilled holes.
Tips for Using a Cordless Drill
- Choose the Right Bit: Ensure you’re using the correct type and size of drill bit for your material.
- Adjust the Clutch: Set the clutch to the appropriate torque to avoid over-driving screws or damaging the material.
- Use the Right Speed: Higher speeds for drilling, lower speeds for driving screws.
- Keep Bits Sharp: Regularly sharpen or replace drill bits for efficient drilling.
- Secure Your Work: Clamp down the material you’re working on to prevent it from moving.
- Battery Maintenance: Keep batteries charged and store them properly to extend their life.
What Not to Do with a Cordless Drill
- Overwork the Motor: Avoid running the drill continuously for long periods, which can overheat and damage the motor.
- Use Dull Bits: This can cause the drill to work harder, reducing efficiency and possibly damaging the tool.
- Force the Drill: Let the drill do the work; applying excessive force can cause bits to break or damage the material.
- Use Incorrect Settings: Always adjust the speed and torque settings appropriately for the task at hand.